Milling Tools Guide
Quality of cutting edge
A high-quality cutting edge ensures precision and efficiency in milling operations. For example, the Kennametal Conical Cutting Edge Mill is known for its exceptional edge quality. It features a conical cutting edge which provides improved stability and increased metal removal rates. Additionally, the Seco High-Performance Square Shoulder Mill offers an exceptionally sharp cutting edge with precision-ground inserts, resulting in superior performance and extended tool life. Other notable options in this category include the Mitsubishi Materials Ball Nose End Mill with its high-quality carbide material and precise edge geometry, and the Walter Xtra-tec Insert Drill
featuring a diamond-coated cutting edge for enhanced wear resistance and performance.
Material and hardness
Different materials require specific types of milling tools that are designed to withstand their hardness levels. For example, when working with soft materials such as wood or plastics, high-speed steel (HSS) milling tools are ideal due to their toughness and capability to withstand lower operating temperatures. Some noteworthy products in this category include the DEWALT DW1361 Titanium Pilot Point Drill Bit Set, featuring titanium coating for strength and durability, and the Bosch CO2143 Cobalt Metal Drill Bit Set, which is made from M42 cobalt steel for high-speed drilling.
On the other hand, when dealing with harder materials like ferrous metals, stainless steel, or even exotic alloys, carbide or solid carbide milling tools are more suitable. These tools feature superior hardness and wear resistance to accommodate the demanding machining requirements. For instance, the SpeTool Carbide End Mill Set, crafted out of superfine particle tungsten steel, offers excellent hardness and heat resistance for cutting ferrous materials. In the solid carbide segment, the OSCARBIDE 1/8" Shank Carbide Flat Nose End Mill CNC Router Bit
stands out with its micro grain carbide material suitable for hardened steel, stainless steel, cast iron, etc.
Diameter
The diameter of a milling tool refers to the width of the cutting edge. The right diameter will depend on the specific milling task and the material being machined. Smaller diameter tools are generally used for intricate and detailed work, while larger diameter tools are more suitable for roughing or removing material quickly.
In terms of specific products, there are various milling tools available on the market that cater to different diameters. For smaller diameter projects, the 'Micro 100' solid carbide milling tool with a diameter of 1/16 inch is an excellent option. It is designed for precise and fine milling tasks, providing high accuracy and surface finish. For medium-sized diameters, the 'YG-1' carbide end mill with a diameter of 1/4 inch delivers both versatility and durability. It is capable of handling a wide range of materials and offers efficient cutting performance. Finally, for larger diameter projects, the 'Cobra Carbide' indexable milling cutter in 2 inches diameter offers exceptional strength and stability. Its carbide inserts ensure long-lasting performance, while the strong body design allows for heavy-duty machining.
Shank type
The shank of a milling tool refers to the portion that is inserted into the milling machine. There are several different shank types available, each designed to be compatible with specific machines and applications.
One common shank type is the straight shank. This type of shank features a cylindrical or straight shape, allowing easy insertion into a collet or chuck. Products such as the Bosch IM0010 Impact Step Drill Bit or the Proxxon 28608 Heavy Duty Thin Profile Straight Shank End Mill Set
are excellent examples of straight shank milling tools. Another popular option is the Tapered shank, which gradually narrows towards the end and is commonly used in machining operations that require high precision. The Accusize Industrial Tools MT3-MT2 Taper Adapter or the Melin Tool AMG-DP-M-B Spec-SS Carbide Ball Nose End Mill
are reliable choices for tapered shank milling tools. It's important to ensure that the chosen milling tool has the appropriate shank type for seamless compatibility with your machine.
Coating
One popular type of coating is the TiAlN coating. The TiAlN coating is a multi-layered coating known for its excellent wear resistance, high thermal stability, and low coefficient of friction. This makes it suitable for a wide range of materials, from steels to stainless steels, and even difficult-to-machine materials like titanium and nickel-based alloys. Some examples of milling tools that come with the TiAlN coating include the YG-1 GMF45 series and the Melin Tool A-VMG series.
Another notable coating is the ZrN coating, which stands for zirconium nitride. The ZrN coating provides high hardness, making it ideal for milling applications involving high-speed and hard materials such as hardened steels. Milling tools with the ZrN coating offer improved heat resistance and can increase tool life significantly. Notable examples of milling tools featuring the ZrN coating are the Osg EXOPRO PHXINK stub series
and the SMAKD Carbide End Mill series. These tools are designed to deliver outstanding performance and durability in demanding milling tasks.
Number of flutes
The number of flutes on a milling tool refers to the number of cutting edges it has. Tools with a higher number of flutes generally provide improved chip evacuation and increased feed rates, resulting in a smoother and more efficient cutting process. On the other hand, tools with a lower number of flutes offer higher cutting speeds and are ideal for applications where chip evacuation is not a primary concern.
In the market, milling tools can be found with different numbers of flutes, ranging from 2 to 6 or more. For example, Melin Tool AXMG45 Series features 2 flutes, making it suitable for high-speed machining and aluminum materials. On the other hand, Niagara Cutter N53921 features a robust 6-flute design, making it ideal for heavy-duty milling and titanium applications. The marketplace also offers an extensive range of options with 3 or 4 flutes, such as LMT Onsrud 65-080, recommended for cutting wood, plastic, and non-ferrous metals, or SG Co Laravel Cristal end mill
, designed for general-purpose milling on a variety of materials.
Helix angle
The helix angle refers to the angle between the cutting edge of the tool and a plane perpendicular to the axis of rotation. This angle is essential as it determines the efficiency, stability, and chip removal performance of the cutting tool.
In the market, milling tools with different helix angles are available to suit various applications. For general purpose milling, products like the HSS High Helix End Mill could be considered. These end mills typically have a helix angle between 30 and 60 degrees and are well-suited for quicker chip evacuation and improved surface finishes. On the other hand, for specialized applications like high-speed machining, Carbide High Helix End Mills with helix angles ranging from 45 to 60 degrees can provide the necessary stability and chip clearance to prevent issues like vibration and tool wear.
Overall length
The length of the tool affects the rigidity and stability during milling operations, and it also determines the maximum reach of the tool. For smaller, more precise milling tasks, a shorter overall length is generally preferred to ensure better control and accuracy. On the other hand, longer overall lengths are beneficial for reaching deep pockets or working on larger projects. It is crucial to match the overall length of the milling tool to the specific task at hand to achieve optimum performance and desired results.
One example of a milling tool suited for smaller and more precise tasks is the YG-1 E2039 series Solid Carbide Corner Radius End Mill
. With an overall length of 2-1/2 inches, this tool offers excellent rigidity and control for intricate milling operations. For longer overall lengths and deeper reach, the Widia Hanita 4505 series Solid Carbide Square End Mill
is a suitable choice. The overall lengths in this series range from 4 to 5-3/4 inches, making it ideal for heavy-duty milling tasks with larger workpieces. These examples showcase how the overall length of milling tools play a vital role in selecting the best tool for the job at hand.
Reach length
The reach length refers to the maximum depth that the milling tool can reach inside a workpiece. This is especially crucial when working on projects that require deep cavity or pocket milling.
One high-quality milling tool that offers an impressive reach length is the YG-1 E5974 series carbide ball nose end mill. It features a reach length of 2.5 inches, making it suitable for deep milling operations. Another option to consider is the Melin Tool VBMG5PG3030-C2 carbide end mill with a reach length of 3 inches. These tools provide a competitive advantage when working on projects that demand milling at deeper depths.
It's worth noting that reach length is available in various options on the market, ranging from standard to extra-long tools. For instance, there are milling tools with reach lengths of 1 inch, 2 inches, 4 inches, and even longer. When selecting the best milling tool, it's crucial to determine the specific reach length required for your project and choose a tool accordingly. Always ensure the tool's reach length meets the depth requirements of your milling application for optimal results.
Flute length
The flute length refers to the length of the cutting edge on the end mill or drill bit. It plays a crucial role in determining the depth to which the tool can cut or drill into the material.
For instance, if you are working with materials that require deeper cuts, such as hardwood or aluminum, it would be advisable to opt for milling tools with longer flute lengths. In this category, the Niagara Cutter - STB440M Series Solid Carbide End Mill stands out with its flute length of up to 4 inches, ensuring efficient cutting in deeper slots or cavities.
On the other hand, for tasks that require shallower cuts, such as working with thin sheet metal or plastics, choosing milling tools with shorter flute lengths would be more appropriate. In this segment, the AUTOTOOLHOME 1/8" Shank Micro Drill Bits
are worth considering, as their flute length of 1/2 inch provides precise drilling without risking over-penetration or damage to the material. Keep in mind that there are numerous products available in the market for different flute length requirements, so it is vital to match the right tool to your specific needs.
Cutting depth
The cutting depth refers to the depth at which the milling tool engages with the workpiece, impacting the efficiency and accuracy of the cutting process. Different projects may require varying cutting depths, so it is crucial to select the appropriate milling tool. For example, the Melin Tool AXMG45B Carbide Square Nose End Mill offers a maximum cutting depth of 1 inch, making it suitable for applications that require milling at relatively deeper depths. Another option is the Yonico 34251-SC CNC Router Bit Set, which provides a variety of router bits with different cutting depths ranging from 1/8 inch to 1/4 inch, catering to various project requirements. These products are examples of milling tools that cater to specific cutting depth needs.
Applicable materials (e.g. metal, wood, plastics)
Different materials like metal, wood, and plastics require specific types of milling tools to ensure optimum performance and quality of the end result.
For metal milling, solid carbide end mills are a great choice. These tools are highly durable and offer excellent performance on metals such as steel and aluminum. Products like the Keo SDE series which feature coatings such as TiN or TiAlN can provide extended tool life and improved performance.
When working with wood, router bits are the preferred choice. These tools come in various shapes and designs to achieve different woodworking tasks. For instance, a straight router bit like the Whiteside 1073
is ideal for removing large amounts of material, while a flush trim bit like the Freud 42-580
is perfect for trimming edges with precision.
For plastics, high-speed steel (HSS) end mills are commonly used. These tools offer excellent heat resistance and can work well with materials like acrylic, polycarbonate, and PVC. Products such as the Melin Tool EMG-B Carbide Micro Ball End Mill with a carbide substrate can provide increased hardness and durability.
Durability
Look for tools made from high-quality and durable materials such as carbide or cobalt. One excellent example is the Dremel 9901 Tungsten Carbide Cutter, which features a carbide construction that offers exceptional durability and long-lasting performance. Another durable option is the Melin Tool Solid Carbide End Mills, renowned for their strong and wear-resistant construction. Additionally, consider tools with coatings like TiN (Titanium Nitride) or TiAlN (Titanium Aluminum Nitride) as they further enhance durability and provide resistance against wear and abrasion. Some reliable options featuring these coatings include the YG-1 Alu-Power End Mill Series and the Accupro Performance Series carbide end mills. By opting for tools with superior durability, you can ensure they will withstand the rigors of milling operations, delivering reliable performance over time.

Tolerance level
It refers to the maximum acceptable amount of deviation from the desired measurement in the machining process. A lower tolerance level indicates a more accurate milling tool while a higher tolerance level allows for some degree of flexibility. For precision tasks where tight tolerances are required, it is essential to choose tools with a low tolerance level such as the YG-1 ER Mill E564 VC-2
that offers a tolerance of +/- 0.003mm. On the other hand, for less critical projects that allow for more deviation, tools with a higher tolerance level like the Accupro Solid Carbide Ball End Mill with a tolerance of +/- 0.008mm can be suitable. The market provides a range of milling tools with varying tolerance levels to cater to different machining needs.



Runout
Runout refers to the degree of deviation from a perfect circular rotation in a spindle, which can lead to less accurate machining and reduced tool life. To ensure optimal performance, it is essential to select milling tools that have low runout values.
One example of a milling tool with low runout is the 'S72V-MVX Shoulder Milling Cutter' by Sandvik Coromant. This shoulder milling cutter features a low runout value of only 0.02 mm, ensuring high precision and accuracy during machining operations. Another excellent option is the 'APT Carboloy Top-On Insert Face and Side Milling Cutters
' by Kennametal. These milling cutters have a maximum runout of 0.004 mm, providing exceptional surface finishes and extended tool life.
When considering different milling tools on the market, it is helpful to divide them into two groups based on runout values. Group A includes milling tools with runout values below 0.05 mm, such as the mentioned Sandvik Coromant S72V-MVX Shoulder Milling Cutter. Group B consists of tools with runout values between 0.05 mm and 0.1 mm, like the 'Kyocera WF-Series Aluminum Roughing End Mills' with a runout of 0.07 mm.
Type of milling tool (end mill, face mill, ball nose, etc.)
There are various types of milling tools available on the market, each designed for specific applications. Some of the most common types include end mills, face mills, ball nose mills, and slot drills.
For example, if you are looking for an end mill, YG-1 E7889 High Speed Steel (HSS) Ball Nose End Mill
could be a great option. This particular end mill is made from High Speed Steel and has a ball nose design, making it suitable for various contour milling and profiling applications. On the other hand, if you need a face mill, the Accusize Industrial Tools 3" Indexable Face Shell Milling Cutter
is worth considering. It features a 4-flute design and can accommodate a variety of insert styles, providing versatility and efficient milling performance.
In summary, when choosing the type of milling tool, you need to consider the specific requirements of your project. Whether you require an end mill, face mill, ball nose mill, or any other type, there are various products available that cater to different milling needs. Be sure to review each tool's specifications to ensure it aligns with your desired machining requirements.
Conventional or high-speed performance
Conventional tools, such as solid carbide end mills, are well-suited for general milling operations. For example, the YG-1 E5974 Carbide Ball Nose End Mill provides excellent standard performance with a five-flute design that enhances cutting efficiency.
On the other hand, if you need to tackle high-speed milling applications, then high-speed performance tools are your best bet. These tools are designed to withstand higher speeds and deliver superior performance. For instance, the Micro 100 RMEM-420-2X Modified For Slotted Groove Milling Tool
is built for high-performance milling with its advanced design and optimized chip evacuation capabilities.



Use for roughing or finishing
Roughing tools are typically designed for removing large amounts of material quickly and efficiently. They are more suitable for rough machining operations and are often characterized by their high metal removal rates. Examples of roughing milling tools include the 'Adirondack Macromills 30302
', which is designed for heavy-duty roughing applications. It features a 3-flute design and a large core diameter for optimized performance.
On the other hand, finishing tools are intended for achieving high surface quality and dimensional accuracy. They are engineered to generate fine finishes and minimal tool marks. A reliable example is the 'Bennet High-Finish Mills 20450
'. This tool features a 4-flute design, ensuring excellent finish and minimal vibration. The multi-layer coating on the tool provides enhanced wear resistance, enabling prolonged tool life during finishing operations.
Segmenting the market further, we can categorize milling tools into different groups based on their specific applications. For roughing, the 'Gorilla Super Rougher' and 'Monster Rougher
' exemplify the innovative cutting edge geometries and carbide grade versatility know-how. These tools allow for increased feed rates and are ideal for high-performance rough milling of various materials.
For finishing, the 'Niagara Finishing Mills' stand out with their advanced flute designs ensuring smooth and precise cuts. Available in multiple flute configurations, such as 3-flute or 5-flute, these tools offer greater flexibility when achieving desired finishing results.
Compatibility with specific milling machines
Different milling machines have different specifications and requirements, so selecting tools that are specifically designed for your machine can ensure optimal performance and productivity. For example, if you have a CNC milling machine that operates at high rotary speeds, you'll want to look for milling tools that can handle high cutting speeds without causing excessive wear or material deformation. One such tool that works well with high-speed CNC milling machines is the OSG Exocarb® Aero UVX-R
. Designed for high-speed machining of aerospace-grade materials, it features a special corner design and polished flute to reduce cutting forces and heat generation, making it an ideal choice for compatibility with high-speed milling machines.
Insert or solid carbide type
Inserts are practical and cost-effective as they offer replaceable cutting edges, reducing the need for frequent tool changes. A popular insert milling tool is the 'Sandvik Coromant CoroMill 390', a versatile tool that provides high productivity with its low cutting forces and helical cutting edges. Another notable option is the 'Iscar Helido F90LN-M25' insert cutter, which features a unique design incorporating an aluminum body for improved deflection and clearance. On the other hand, solid carbide tools offer exceptional rigidity and are ideal for stable machining operations. A reliable product in this category is the 'Kennametal Series HPHV AlTiN
' solid carbide end mill, crafted using high-performance carbide for longevity and precision.⠀
Type of milling operation (milling, drilling, grooving, etc.)
Each type of operation requires a specific tool to achieve the desired results.
For milling operations, one example of a high-quality tool is the Kennametal Mill 4-15. This tool is specifically designed for high-performance roughing and finishing, offering efficient material removal rates and excellent surface finishes. It features a four-flute design and variable pitch that reduces harmonics, allowing for smoother cutting and increased productivity.
For drilling operations, the Seco SD200A
is an excellent choice. This drill features optimized geometries and advanced drilling strategies, ensuring high metal removal rates and outstanding hole quality. It is specifically designed for various applications, including drilling in steels, stainless steels, and cast iron.
For grooving operations, the Iscar GSF GFF
is a great option. This tool offers a wide range of groove widths and depths, providing versatility and flexibility. It features a high-precision geometry and chip breaker design for improved chip control and excellent surface finish.
These examples highlight the importance of choosing the right milling tool based on the specific type of operation undertaken. Other factors such as material, cutting parameters, and machining conditions should also be taken into account to ensure optimal performance.
Accuracy and precision
It is essential to ensure that the milling tools you choose are capable of delivering precise cuts and maintaining accurate dimensions. For example, GRBL Control DIY CNC Machine Kit offers high precision with a positioning accuracy of 0.08mm-0.1mm and a repeatability of 0.08mm. Similarly, the Precision ER25 Collet Chuck Set is known for its accuracy, featuring a runout of less than 0.0003".
In the market, milling tools can be divided into different segments based on the precision they offer. The first group includes entry-level milling tools suitable for basic tasks. Products such as the Proxxon 37110 MICRO Mill MF 70
are excellent choices for beginners, providing accuracy of up to 0.02mm. The second group consists of intermediate-level milling tools that offer greater precision and versatility. Examples include the JET JMD-18 350018 Mill/Drill Machine
, which offers down feed scale that ensures accurate depth measurements. Lastly, professional-grade milling tools such as the Haas VF-2SS Super Speed CNC Vertical Mill
are designed for advanced users who prioritize utmost precision, featuring a positioning accuracy of +/- 0.002" and repeatability of +/- 0.0002".
Chip evacuation capability
This capability refers to the tool's ability to effectively remove chips or waste material from the cutting area during the milling process. Tools with poor chip evacuation capability can result in chip build-up, leading to decreased accuracy, tool wear, and increased machine downtime. To ensure efficient chip evacuation, it is crucial to opt for tools specifically designed for this purpose. One such tool is the 'Sandvik Coromant CoroMill 600,' known for its exceptional chip evacuation performance due to its unique insert geometry and integrated coolant channels. Another suitable option is 'Walter H4040328-M-M84DP wiper inserts,' which feature specialized geometry that aids in chip breaking and evacuation, ensuring a smooth and uninterrupted milling process.
Resistance to heat and wear
Heat and wear are primary concerns as milling operations produce significant amounts of heat and can gradually wear down the tools. One notable example of a milling tool with exceptional resistance to heat and wear is the Kyocera DLC (Diamond-Like Carbon) Mill. Featuring a diamond-like carbon coating, this tool offers extraordinary hardness, superior wear resistance, and exceptional thermal stability. It can effectively withstand high temperatures and maintain its sharpness for a prolonged period, resulting in extended tool life and reducing the need for frequent tool changes.
In addition to the DLC Mill, another category of milling tools renowned for their resistance to heat and wear is the Carbide End Mills. Available in various types such as solid carbide, coolant-through, and roughing mills, these tools are manufactured from high-quality carbide materials that provide excellent resistance to heat and wear. Some popular carbide end mills include the Melin Cobalt Performance EXM Series
, which boasts an AlTiN coating for increased hardness and heat resistance, and the Dormer S803 Solid Carbide End Mill, designed with a TiAlN coating to enhance tool life and reduce wear. These carbide end mills exhibit the capability to excel under high-temperature conditions while maintaining their cutting-edge performance.

Vibration control
Vibration can negatively affect machining accuracy and tool life, so selecting tools with effective vibration control is crucial. One recommended product for this purpose is the 'Makita RT0701C' router kit, which features a soft start feature that reduces start-up torque and a variable speed control dial for precision routing. Additionally, the kit includes two different base options – a fixed base and plunge base – allowing users to choose the most suitable option for their specific application. Another product to consider is the 'DEWALT DWP611' compact router, renowned for its exceptional vibration control. This router offers a full-time electronic feedback control system that maintains motor speed throughout the cut, ensuring consistent results. Its adjustable ring enables depth changes, while the dual LED lights provide ample visibility for accurate cutting.
Cutting speed
It refers to the speed at which the tool makes a cut in the material being milled. The cutting speed is typically measured in surface feet per minute (SFPM) or meters per minute (MPM). To ensure optimum performance, it is crucial to select milling tools that are capable of achieving the required cutting speed for the specific material you are working with.
For high-speed milling applications, Kyocera SGS Precision Tools Z-Carb EM Solid Carbide Square End Mill
is a great choice. These square end mills are designed for aggressive high-speed machining, delivering excellent cutting speeds of up to 900 SFPM. They feature variable index geometry which reduces vibration and enhances chip control, resulting in improved surface finish. Another high-speed milling option is the GARR carbide end mill series by Garr Tool. These end mills are available in various cutting diameters and offer exceptional speeds of up to 1200 SFPM, making them ideal for cutting through aluminum and other non-ferrous materials.
Feed rate
The feed rate refers to the speed at which the milling tool moves along the workpiece during the cutting process. Opting for a milling tool with a higher feed rate can improve efficiency by reducing machining time while maintaining cutting precision.
For applications requiring high feed rates, the Widia Hanita VariMill GP 4GDL
stands out. With a high feed rate capacity of up to 25 meters per minute, this milling tool allows for rapid material removal while ensuring accuracy and surface finish quality. In addition, its carbide construction offers excellent wear resistance and toughness, enhancing tool longevity. For those needing more versatility, the Iscar-Milling EHML-CFE
milling tool allows for both high feed rates (up to 20 meters per minute) and flexibility in various machining operations such as roughing, finishing, and slotting. This provides users with the option to work with different materials and applications without sacrificing performance or compromising on quality.
Other milling tools available in the market can be divided into three segments; high feed milling tools, variable helix milling tools, and chamfer milling tools. High feed milling tools, such as the Kyocera-Mill4Feed
, are designed specifically for high feed rates, ensuring efficient material removal at rapid speeds. Variable helix milling tools, such as the Sandvik Coromant CoroMill 390, feature a multi-flute design and a variable helix angle that supports high feed rates for diverse machining tasks. Chamfer milling tools, like the Melin MSC
series, prioritize precise chamfer formation while providing a reasonable feed rate for creating accurate, beveled edges.
Chip load
Chip load refers to the amount of material that is being removed by each flute of the milling tool during each rotation. It is usually measured in inches per tooth (IPT) or millimeters per tooth (mm/tooth).
For high performance milling and efficient material removal, it is important to select milling tools with an appropriate chip load for the desired application. Insufficient chip load can result in poor surface finish, reduced tool life, and inefficient cutting, while excessive chip load can lead to tool vibration and breakage.
In the market, there are several groups or segments of milling tools available that cater to different chip load requirements. For example, Indexable cutting inserts like the Sandvik Coromant RCKT 07T3MO
provide an ideal chip load for general purpose milling operations. Solid carbide end mills like the Micro 100 MEFM-010-200-005Z
offer precise chip load control for fine finishing and contouring. Higher chip load requirements for heavy-duty milling can be met with roughing end mills like the Melin Tools AMG-M42-JC6 that have multiple flutes and wide chip evacuation capabilities. It is important to carefully assess the chip load requirement for your specific application and choose milling tools accordingly.
Cutting edge geometry
This determines the shape and angle of the cutting edges on the tool, which can significantly impact the performance and results of your milling operations. High-speed steel (HSS) end mills with standard cutting edge geometry are versatile options suitable for most general-purpose milling applications. They are often available with various coatings, such as titanium nitride (TiN) or aluminum titanium nitride (AlTiN), which enhance wear resistance and prolong the tool life. For more demanding tasks, solid carbide end mills with advanced cutting edge geometry, such as variable helix or variable pitch, are recommended as they provide superior material removal rates and reduced vibrations. Examples of solid carbide end mills with excellent cutting edge geometry include the Kennametal HARVI™ I TE series, the Guhring GW-C
series, and the OSG VGx End Mill series. These tools ensure efficient and precise milling, making them suitable for both roughing and finishing applications.
Flute shape
The flute shape determines the chip evacuation, cutting edge strength, and rigidity of the tool. There are various types of flute shapes available on the market, each offering different advantages for specific applications.
One common flute shape is the square end mill. This type of tool has a straight cutting edge with square corners, making it suitable for general milling applications. It provides good cutting performance and is versatile for a wide range of materials. An example of a square end mill is the Ougar8 4 Flutes Square Nose End Mill, which features four flutes for efficient chip evacuation and available in various sizes.
Another flute shape to consider is the ball nose end mill. This tool has a rounded end, resembling a ball, and is suitable for contour machining and 3D sculpting. The ball nose end mill creates smooth curves and is excellent for creating intricate designs. An example of a ball nose end mill is the YUFUTOL Carbide Ball Nose End Mill, which has a durable carbide construction and is available in different diameters.
If you're working with wood materials, it is recommended to choose a mill with a downcut spiral flute shape. This type of tool pulls the chips downward, resulting in cleaner edges and prevents chip-out on the top surface. One option to consider is the Freud 70-105 Down Spiral Solid Carbide Router Bit, which features a three-flute design for smooth cuts and reduced tear-out in wood materials.

By carefully considering the flute shape and choosing the right milling tool, you can enhance your machining capabilities and achieve the desired results for your specific application.
Component features (e.g. chipbreaker, coating, coolant hole)
Several key component features should be considered such as chipbreaker, coating, and coolant hole. The chipbreaker plays a crucial role in chip control and can improve the tool's ability to remove material quickly and cleanly. Recommended products in this category include the Sandvik Coromant CoroCut QF B and Kennametal Mill 4-11. Their chipbreakers are specifically designed to enhance chip control, reducing the risk of chip build-up and increasing productivity.
Additionally, the coating of the milling tool is important as it provides protection against wear and extends tool life. Choose tools with high-quality coatings like titanium nitride (TiN), titanium carbonitride (TiCN), or aluminum titanium nitride (AlTiN) for improved performance. The Mitsubishi Materials MP9005 and Iscar IC808 are excellent examples of milling tools with durable and high-performance coatings. These tools are designed to withstand the high temperatures generated during machining and provide optimal performance in a variety of materials.
Finally, the presence of a coolant hole in a milling tool aids in efficient chip evacuation and heat dissipation, leading to increased tool life and productivity. Look for tools like the Sutton Tools Imperial Bolt, which features a coolant hole for improved chip evacuation and reduced tool wear.
Expert recommendations
Experts in the field suggest various cutting tools that offer exceptional performance and durability, ensuring efficient and precise milling operations. One such recommendation is the Seco Square® 6 milling cutter
, known for its superior chip evacuation and stability. With its robust design and innovative cutting edge geometry, it enables high metal removal rates in various materials. Another expert-recommended tool is the Kennametal Mill 4™-12KT end mill, which features a unique double-sided round insert. This design offers fantastic versatility and reduces cutting forces, contributing to improved stability and productivity.
Within the milling tools market, products can be categorized into different segments based on their specific features and applications. Some groups include face mills, shoulder mills, and high-performance end mills. High-quality face mills like the Walter F2339 Finishing End Mill
are the expert preference for achieving precise face milling and mirror-like finishes. For shoulder milling, the Iscar HCM D0907
series stands out with its carbide inserts and multi-flute construction, providing excellent performance in roughing and semi-finishing applications. In the high-performance end mills segment, Kyocera SGS 32664-C1
milling cutters deserve a special mention for their exceptional cutting speeds and feed rates, assisted by their rugged substrates and high helix angle.
Operational safety precautions
To guarantee the protection of operators, it is crucial to select tools that offer advanced safety features. For instance, Makino's a61nx-5E
milling machine is equipped with safety measures including an ergonomic design that minimizes fatigue and reduces strain on the operator's body, and a fully enclosed safety guard that prevents any unauthorized access to the machine during operation. Additionally, the Haas DM-2
milling machine boasts safety features such as an emergency stop button that instantly halts all machine processes to prevent any potential mishaps, as well as a high-visibility, interlocked spindle safety guard that ensures the operator's safety during operation. It is recommended to consider milling tools that offer similar safety precautions to eliminate any safety hazards in the workplace.
Ease of maintenance and cleaning
Look for tools that are designed for easy disassembly, with removable parts that can be cleaned separately. For example, the RedLine Tools Carbide End Mill boasts a removable shank and solid carbide construction, allowing for easy cleaning and extended tool life.
Another option to consider is the Melin Tool RCMG Carbide End Mill. This tool features a unique design with a coolant through hole, allowing for efficient chip evacuation and easier cleaning. Additionally, its solid carbide construction ensures durability and resistance to wear.
For those in need of high-speed cutting tools, the YG-1 Alu-Power HPC Solid Carbide End Mill is worth looking into. With a special coating designed for aluminum cutting and an open flute design for easy chip evacuation, this tool offers both maintenance and cleaning convenience.

In the market, there are various segments of milling tools available. Some common segments include high-performance end mills, corner rounding end mills, and roughing end mills. Notable products that correspond to these segments are the HARVI™ Ultra 8X High-Performance Solid Carbide End Mill for high-performance milling, the SGS 31867 Solid Carbide Corner Rounding End Mill for corner rounding applications, and the Kennametal A9 SeriesTM Roughing End Mill for roughing operations. All these tools are designed with convenience in maintenance and cleaning, helping to keep your milling setup in top shape.
Price
The price of milling tools can vary depending on factors such as the material, accuracy, and size. Some affordable options to consider include 'Hakkin 10pcs Carbide End Mill Set' which is designed for cutting metals and has a diameter range between 1.0mm to 3mm, and the 'Genmitsu CNC Router Bits 1/8” Shank 4-PCS' which are budget-friendly end mills suitable for wood and acrylic applications. Alternatively, those seeking high-end milling tools can opt for the 'YG-1 E5246 Carbide Ball Nose End Mill, Uncoated (Bright) Finish, 30 Deg Helix, 4 Flutes', which offers excellent precision and works well on materials like steel and titanium. It's crucial to evaluate the features and specifications provided by each product to ensure you're selecting the best milling tools according to your price range.
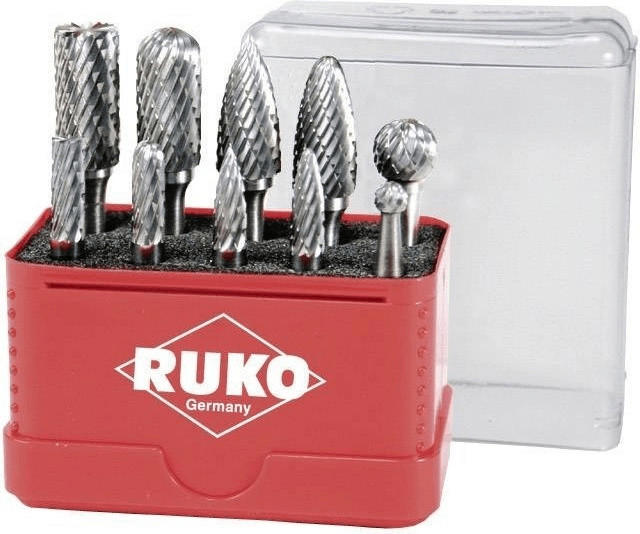
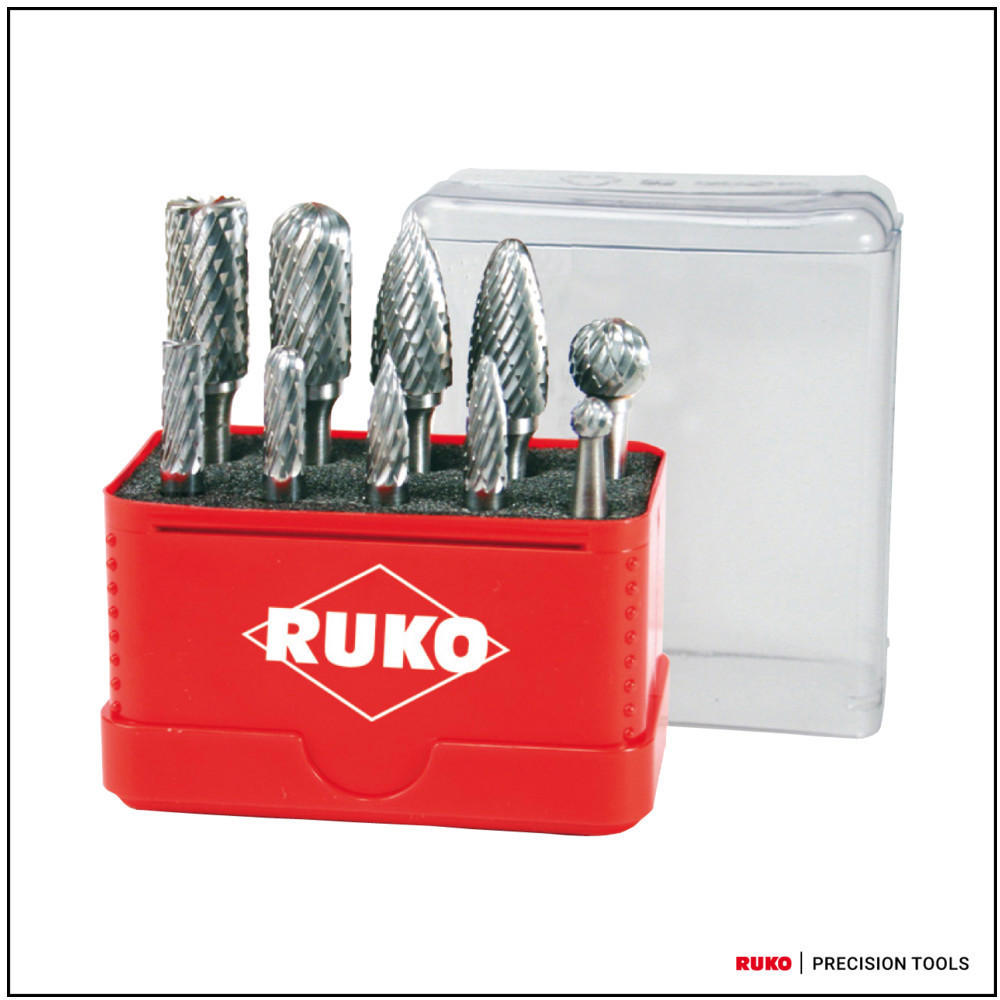
Variety of brands
This allows for a comparison of the different features, quality, and performance each brand offers. For instance, Makita is a well-known brand that offers a range of milling tools suitable for various applications. Their products are known for their durability and high-quality performance. Another reputable brand is Bosch, which offers milling tools with ergonomic designs, ensuring comfortable and precise use. However, one disadvantage of Makita and Bosch tools is their relatively higher price compared to budget brands such as Black+Decker. While Black+Decker tools may provide excellent value for money, they may lack advanced features present in more premium brands.
Other notable brands in the market include DeWalt, which offers milling tools with powerful motors and precise cutting capabilities. DeWalt also specializes in cordless milling tools, providing versatility and ease of use. Milwaukee is another recognized brand known for its innovative milling tools featuring advanced technologies like brushless motors for enhanced power and longer runtime. In terms of product segments, there are both handheld and benchtop milling tools available. For example, the Makita RT0701CX7
is a popular handheld router that offers variable speed options, compatibility with various bases for increased versatility, and quick depth adjustments. On the other hand, the Jet 350017
is a widely recognized benchtop milling tool with a powerful motor, precise spindle speed selection, and a robust cast iron construction.
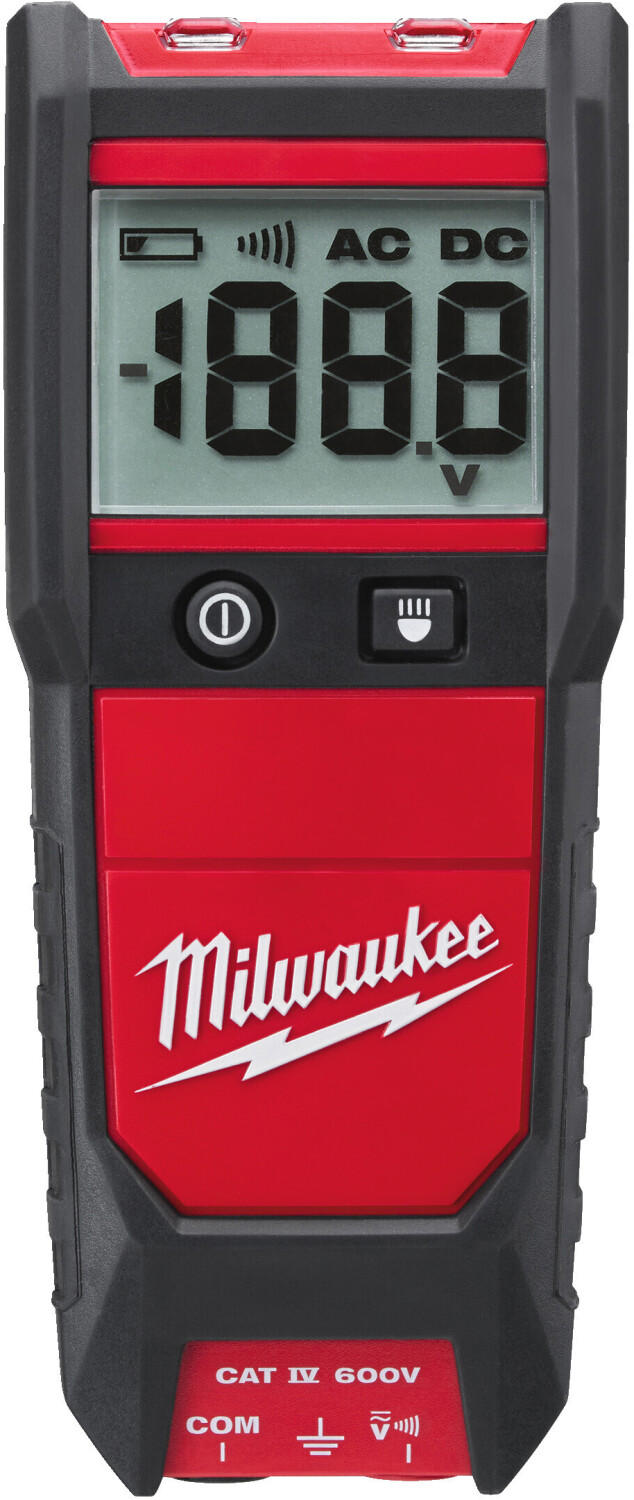
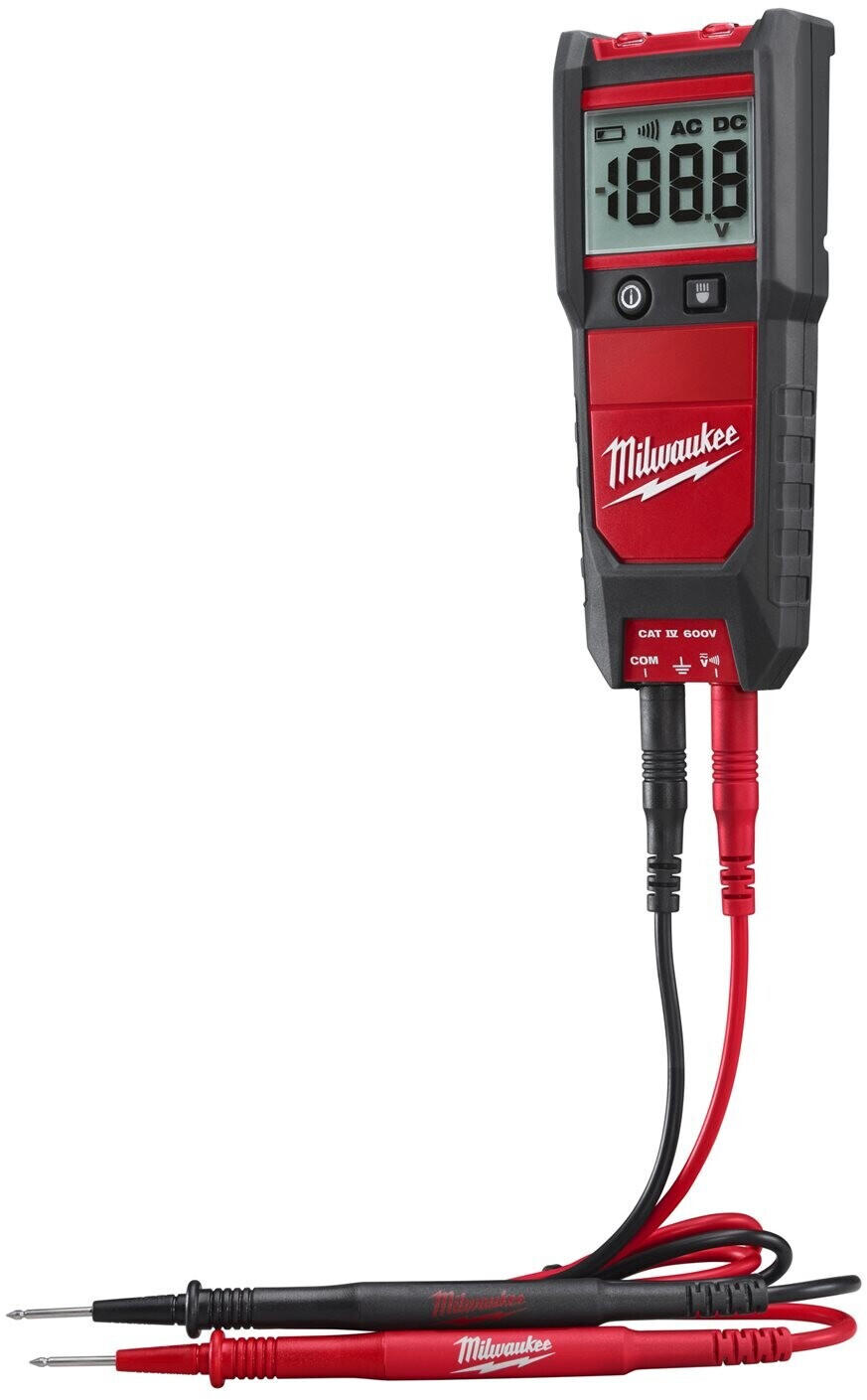
Ultimately, the choice of milling tools brand depends on individual preferences, budget constraints, and the specific requirements of each project. It is important to research the specifications of different brands and carefully evaluate their pros and cons before making a purchase decision.